1. Types of Rubber Used in Manufacturing:
- Natural Rubber (NR): Derived from the latex sap of rubber trees (Hevea brasiliensis). It is known for its elasticity and resilience.
- Synthetic Rubber: Made from petrochemical sources, synthetic rubber types include
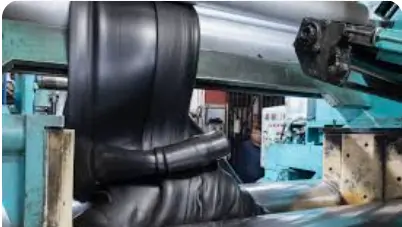
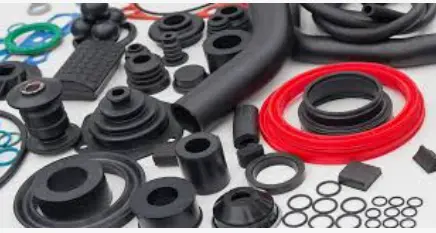
Rubber Manufacturing Process:
The rubber manufacturing process involves several steps:
a. Preparation of Raw Materials:
- Natural Rubber is collected from rubber trees, while synthetic rubbers are produced from petrochemical compounds.
- Rubber may be mixed with various chemicals, such as accelerators, fillers, and plasticizers, to enhance its properties (such as strength, flexibility, and durability).
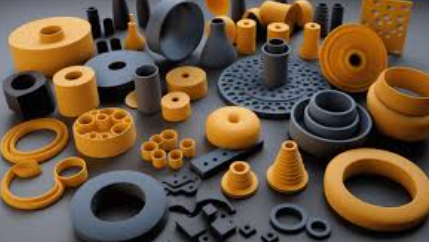

Rubber O-Rings
- Used in mechanical equipment to seal joints and prevent the leakage of fluids or gases, rubber O-rings are circular rubber parts that fit into grooves.
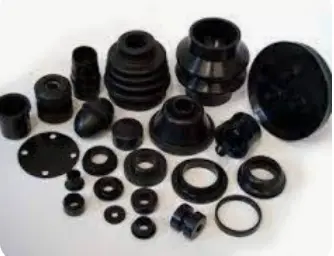
Rubber Grommets
- Grommets are small rubber rings used to protect wires and cables that pass through metal or other materials, preventing wear and tear.
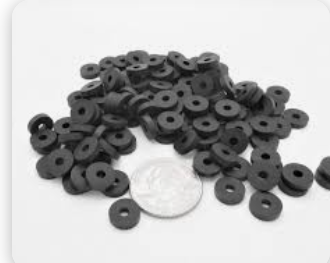
Rubber washers are flat, round pieces of rubber that are used in various applications to provide sealing, cushioning, and vibration dampening. They are often placed between two surfaces to create a seal, prevent leaks, or protect surfaces from damage caused by friction.
Key milestones in our product development
Our milestones include reducing waste, utilizing eco-friendly materials, and enhancing our production processes for a greener tomorrow.
Reduction in waste emissions
Rubber Products Recycled
Recycling rate of rubber materials
Liters of water saved in production
Renewable Energy usage in manufacturing
Tons of rubber recycled
Rubber manufacturing refers to the process of producing rubber-based products from raw rubber materials.

HOW TO MAKE A PRODUCT
Together, with industry leaders to promote sustainable practices in rubber manufacturing.
It sounds like you’re looking for information on how to create or manufacture a rubber product. Here’s an overview of the general process used in making rubber products, from raw material selection to final shaping and curing:
1. Choose the Type of Rubber
- Natural Rubber: Made from latex from rubber trees, has excellent elasticity and resilience.
- Synthetic Rubber: Made from petroleum-based chemicals; different types (like neoprene, silicone, EPDM) have properties suited to specific applications (like resistance to oil, temperature, etc.).
2. Formulate the Rubber Compound
- Compounding: This involves mixing raw rubber with additives to improve its properties (e.g., fillers, plasticizers, antioxidants, vulcanizing agents like sulfur).
- This stage depends on the desired qualities (flexibility, resistance, hardness) of the end product.
3. Mixing and Blending
- Using machinery like internal mixers (e.g., Banbury mixers) or two-roll mills, the ingredients are blended at high temperatures to form a consistent compound.
- The mixed rubber is then rolled into sheets or extruded.
4. Shaping and Forming
- Molding: Different types of molds can be used for shaping, such as compression, injection, or transfer molds.
- Extrusion: For continuous shapes like tubing or profiles, rubber is forced through a die of the desired shape.
5. Vulcanization
- This is the process of heating rubber with sulfur or other agents to cross-link the polymer chains. It makes rubber stronger, more elastic, and more durable.
- The rubber is placed in a heated mold, which initiates the curing process. Timing and temperature control are essential here.
6. Finishing Processes
- Trimming: Excess rubber is trimmed off.
- Surface Treatment: If needed, the rubber surface is treated to enhance appearance, adhesion, or durability.
- Inspection and Quality Control: The product undergoes quality checks to ensure it meets specifications.
7. Packaging and Distribution
- The finished rubber product is cleaned, packaged, and sent for distribution.
Each product type may have unique requirements (e.g., medical-grade rubber vs. automotive rubber), and there are variations in the exact process depending on these requirements. Let me know if there’s a particular type of rubber product you're interested in making or need more detailed steps on a specific process! More information
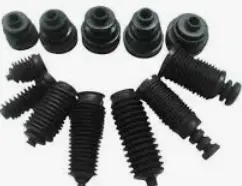

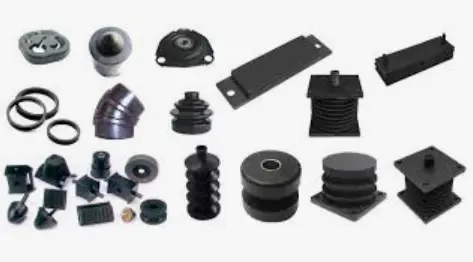
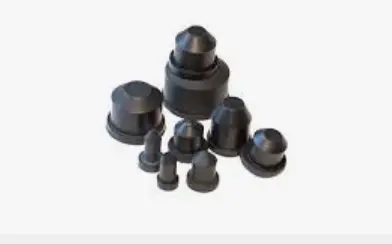
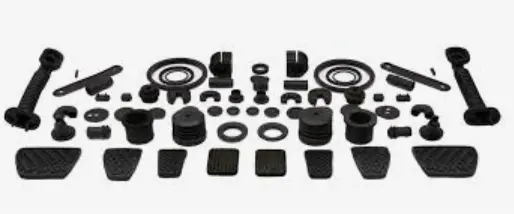
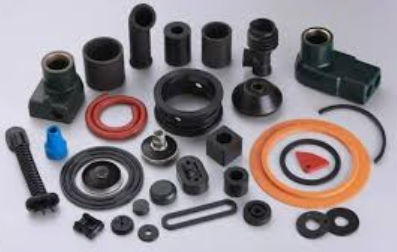
Rubber Manufacturing for a Sustainable Future
Join us in our mission to revolutionize the rubber industry and promote sustainable practices. We focus on creating a greener future through cutting-edge rubber solutions.